What is a dosing system used for?
What is a dosing system used for?
A dosing system is a device that automatically adds a controlled amount of a chemical or other substance to a liquid or gas stream. It is used in a variety of industries, including water treatment, food processing, and manufacturing.
In water treatment, dosing systems are used to add chemicals to control pH, disinfect water, and prevent scale and corrosion. For example, chlorine is dosed into drinking water to kill bacteria, and fluoride is dosed into water to strengthen teeth.
In food processing, dosing systems are used to add chemicals to prevent spoilage, improve flavor, and enhance the nutritional value of food. For example, sulfur dioxide is dosed into wine to prevent oxidation, and ascorbic acid is dosed into juices to preserve freshness.
In manufacturing, dosing systems are used to add chemicals to control the properties of materials, such as viscosity, pH, and conductivity. For example, epoxy resin is dosed with a hardener to cure it, and lubricants are dosed into bearings to reduce friction.
Dosing systems can be either manual or automatic. Manual dosing systems require a human operator to add the chemical, while automatic dosing systems do it automatically. Automatic dosing systems are more precise and efficient than manual dosing systems, and they are often used in large-scale applications.
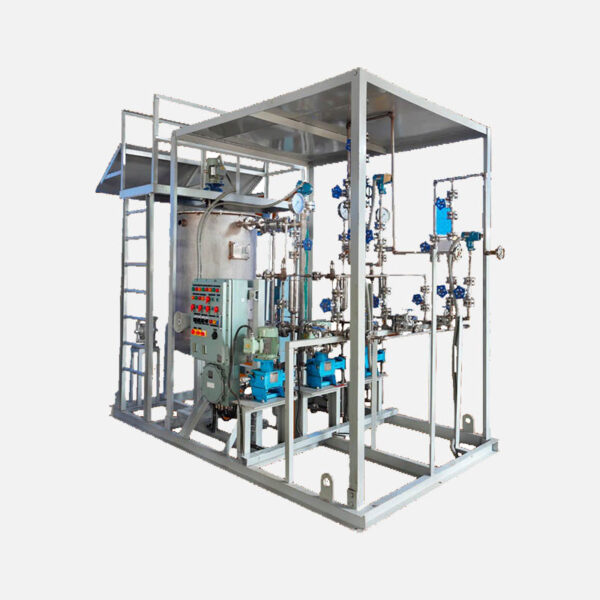
- Positive displacement pumps: These pumps deliver a fixed volume of liquid or gas each time they cycle. They are often used for hydraulically actuated diaphragm pump.
- Proportional pumps: These pumps deliver a variable volume of liquid or gas, depending on the input signal. They are often used for feedback control applications.
- Concentration controllers: These controllers maintain a constant concentration of a chemical in a liquid or gas stream. They are often used in water treatment applications.
Dosing systems are an essential part of many industrial processes. They help to ensure that the right amount of chemicals is added to a process, which can improve product quality, safety, and efficiency.
- Accuracy: Dosing systems can deliver a precise amount of chemical, which is important for maintaining product quality and safety.
- Efficiency: Automatic dosing systems can be more efficient than manual dosing systems, as they can add chemicals without the need for human intervention.
- Safety: Dosing systems can help to ensure that chemicals are added safely, as they can prevent overdosing and spills.
- Compliance: Dosing systems can help to ensure that a company complies with regulatory requirements, such as those for water treatment.
- The type of chemical to be dosed: Different types of chemicals require different types of dosing systems. For example, a positive displacement pump is a good choice for dosing a liquid chemical, while a proportional pump is a good choice for dosing a gas chemical.
- The flow rate of the process: The flow rate of the process will determine the size of the dosing system needed. For example, a high-flow process will require a larger dosing system than a low-flow process.
- The accuracy required: The accuracy required will determine the type of dosing system needed. For example, a high-accuracy process will require a more precise dosing system than a low-accuracy process.
- The budget: Dosing systems can range in price from a few hundred dollars to several thousand dollars. It is important to set a budget before choosing a dosing system.
If you are looking for a way to add chemicals to a process accurately, efficiently, and safely, then a Dosimix Technologies’ dosing system is a good option. There are many different types of dosing systems available, so you can find one that meets your specific needs.
I hope this helps! Let me know if you have any other questions.